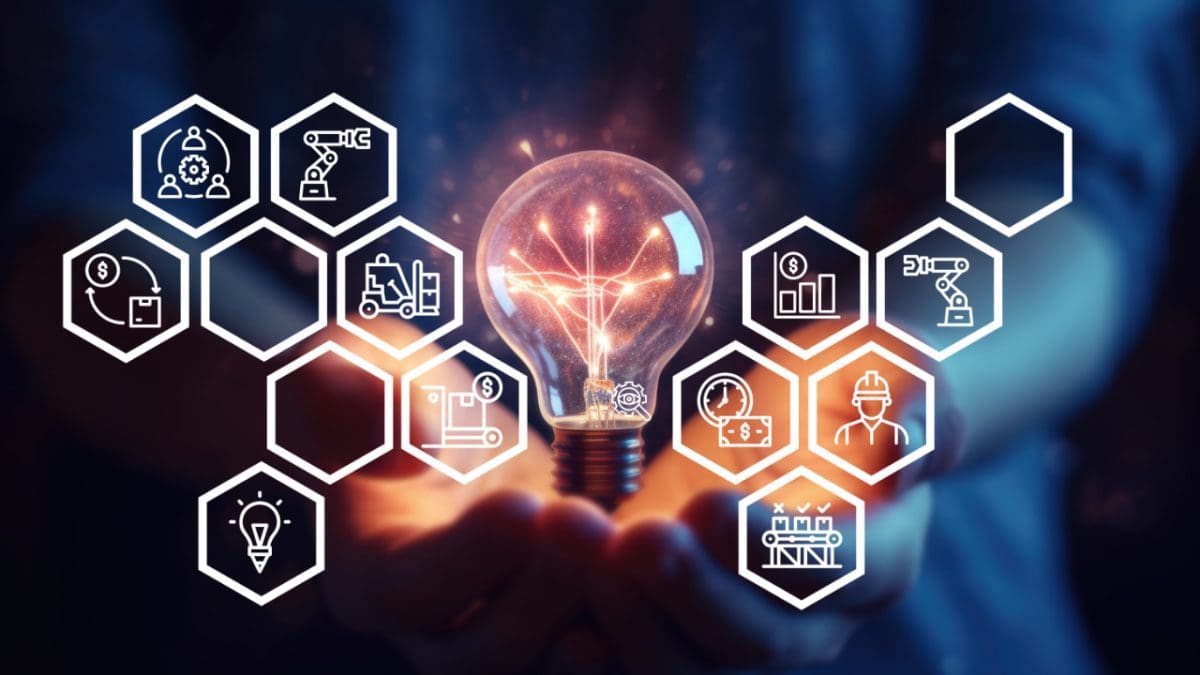
Capacity planning is a game-changer in the delivery industry, enabling companies to optimize their resources and minimize costs. It also plays a pivotal role in meeting customer demand by helping businesses make the best use of their available assets. Today, we’re exploring the fundamental aspects of capacity planning for deliveries and strategies aimed at enhancing efficiency and reducing costs.
Effective capacity planning is especially important for businesses operating in the delivery industry. By carefully evaluating and forecasting demand, companies can align their resources accordingly, ensuring smooth operations and timely deliveries in today’s competitive market. By understanding and implementing capacity planning techniques, delivery companies can ensure that they have the necessary resources available to minimize bottlenecks and avoid delays. The goal is to strike a balance between satisfying customer requirements and optimizing available assets.
Dive into the specifics of capacity planning, including demand forecasting, resource availability, delivery time frames, and service level agreements. In addition, explore strategies for maximizing resources, minimizing delivery costs, and seamlessly integrating capacity planning with demand fluctuations.
By acquiring a comprehensive understanding of capacity planning and implementing the appropriate strategies, businesses can unlock their full potential in the delivery industry.
Understanding Capacity Planning for Delivery
Capacity planning for deliveries involves three essential elements: accurate demand forecasting, assessing resource availability, and establishing appropriate delivery time frames and service-level agreements (SLAs). By effectively managing these factors, delivery and warehouse managers can streamline operations and create a seamless customer experience. This multifaceted process is crucial for optimizing efficiency and ensuring customer satisfaction.
Accurate demand forecasting is the heart of capacity planning. It involves analyzing historical data, market trends, and customer behavior patterns to anticipate future demand. By leveraging advanced analytics and forecasting techniques, businesses can estimate the volume and timing of customer orders more precisely. This helps them allocate resources appropriately, avoiding situations where assets are underused or overloaded. A well-executed demand forecasting results in improved operational efficiency, reduced lead times, and a better customer experience.
Common methods for creating demand forecasts include:
- Barometric Forecasting: Uses current data and statistical analyses to create a demand forecast.
- Trend Projection: Utilizes historical data and growth patterns to create a sales forecast.
- Exponential Smoothing: Incorporates historical data and seasonal variations to create a quantitative forecast.
- Regression Analysis: Incorporates internal and external data into the analysis.
- Econometric Forecasting: Considers the interplay of demand data and external factors to create a demand plan.
Another crucial aspect of capacity planning is assessing the availability of resources. Delivery companies need to assess the capacity of their warehouses or storage facilities to handle incoming inventory and outgoing orders. This assessment includes considering factors like storage space, equipment, and technology needed to handle varying order volumes. By ensuring that resources are aligned with expected demand, businesses can avoid bottlenecks, prevent stockouts, and maintain smooth order fulfillment processes.
Establishing appropriate delivery time frames and SLAs is vital to meet and effectively managing customer expectations. This involves considering factors such as order volume, delivery distances, and any specific requirements or constraints. Capacity planning plays a critical role in helping companies optimize their delivery schedules, efficiently allocate resources, and ensure deliveries are made on time.
Shopify, a top-tier eCommerce platform, handles a massive volume of transactions daily from over 1 million merchants. To accommodate its rapid and unpredictable growth, LinkedIn says Shopify utilizes a flexible capacity planning strategy that capitalizes on cloud services and edge computing. By leveraging these technologies, Shopify can scale its operations seamlessly, deploy updates swiftly, and distribute the workload economically across its global network of servers and data centers. This approach eliminates the need for costly fixed infrastructure and ensures optimal performance for its merchants and customers.
Effective capacity planning for deliveries enables businesses to streamline operations, reduce lead times, and earn consumer loyalty by leveraging advanced technologies and analytics.
Maximizing Resources for Efficient Deliveries
Efficient delivery operations depend on effectively using available resources. This involves evaluating warehouse or storage capacity, analyzing transportation fleet capabilities, and optimizing labor and staffing. By conducting thorough assessments, delivery companies can identify areas for improvement and allocate resources in a manner that boosts efficiency and effectiveness.
When evaluating warehouse or storage capacity, it’s essential to assess the available space and how it’s used. By analyzing the layout, storage systems, and inventory management practices, companies can identify opportunities to better use warehouse operations. This may include reorganizing storage areas, implementing efficient shelving systems, or adopting innovative inventory management technologies to streamline processes and reduce wasted space.
Analyzing transportation fleet capabilities is essential for maximizing resources in deliveries, optimizing fleet performance, and managing costs. By evaluating fleet size, vehicle types, and overall capacity, delivery companies can make informed decisions about route planning, load optimization, and resource allocation. This, plus the use of advanced routing software, enables them to enhance delivery schedules, decrease fuel consumption, and improve overall fleet performance. In addition, optimizing load distribution and matching the right vehicles and drivers to specific delivery requirements allows for better resource use and cost management. Through these practices, companies can achieve efficient deliveries, while minimizing fleet costs and improving customer satisfaction.
Equally important in maximizing resources for efficient deliveries is optimizing labor and staffing requirements. By conducting careful evaluations of workforce needs, delivery companies can determine the right staffing levels and skill sets needed to meet customer demands. This involves analyzing historical data, accounting for seasonal variations, and implementing effective workforce management strategies. By aligning labor resources with delivery needs, companies can achieve maximum productivity, reduce overtime costs, and cultivate a motivated and engaged workforce.
Using technology for inventory management is a powerful method to boost efficiency and lower costs. Advanced inventory management systems offer real-time visibility into stock levels, automate order processing, and enable accurate demand forecasting. By leveraging these technologies, delivery companies can optimize inventory levels, reduce stockouts, and enhance order fulfillment accuracy, leading to faster and more efficient deliveries.
According to AIMMS, Heineken uses a brewing capacity model for optimal allocation of demand to each brewery by considering expected demand and available capacity. The process used to be time-consuming and manual but now is significantly simplified through the use of their software platform.
Implementing automation and robotics in delivery processes can significantly improve efficiency too. Innovations such as automated sorting systems, robotic picking technologies, and autonomous delivery vehicles are revolutionizing the industry. By integrating these advancements into their operations, companies can reduce manual errors, speed up order processing, and enhance overall delivery efficiency.
Minimizing Delivery Costs
Delivery costs play a crucial role in a company’s profitability. To manage and reduce these costs, it’s important to identify the main drivers and implement targeted strategies. By addressing transportation expenses, inventory carrying costs, and labor and overtime expenses, companies can optimize their cost management and achieve significant savings.
Transportation Expenses
Transportation costs play a significant role in delivery operations. To minimize these expenses, companies can try the following strategies:
- Route Optimization and Load Planning: By optimizing delivery routes and consolidating shipments, companies can reduce fuel consumption, minimize mileage, and improve the efficiency of their deliveries. Advanced route planning software and load optimization algorithms can help achieve these goals by identifying the most efficient routes and optimizing the allocation of shipments.
- Mode Selection: Choosing the most appropriate mode of transportation for each shipment can also contribute to cost reduction. Depending on the distance, urgency, and nature of the goods, companies can opt for road, rail, air, or sea transport. Each mode has its own advantages and cost considerations.
- Carrier Negotiation: Building strong partnerships with transportation carriers and negotiating favorable rates can lead to significant cost savings.
- Fuel Efficiency and Maintenance: Managing fuel expenses is crucial in transportation operations. Companies can invest in fuel-efficient vehicles, implement driver training programs to promote eco-friendly driving habits and conduct regular maintenance to keep vehicles in optimal condition.
Inventory Carrying Costs
Inventory management is a critical aspect of minimizing costs. Companies can use the following strategies to reduce inventory carrying costs:
- Effective Demand Forecasting: Accurate demand forecasting empowers companies to maintain optimal inventory levels, preventing both excess stock and stockouts.
- ABC Analysis: Implementing an ABC analysis categorizes inventory based on its value and contribution to overall sales. This allows businesses to focus their attention and resources on high-value items while adopting lean inventory practices for low-value items.
- Vendor-Managed Inventory (VMI): VMI is a collaborative inventory management approach where suppliers are responsible for monitoring and replenishing inventory at customer locations. By sharing real-time sales and inventory data, companies can improve supply chain visibility and efficiency.
- Just-in-Time (JIT) Inventory: JIT inventory management aims to minimize carrying costs by receiving inventory just in time for production or customer orders. By closely aligning inventory levels with actual demand, companies can reduce holding costs associated with excessive inventory and free up capital for other purposes. JIT requires effective coordination with suppliers and reliable logistics to ensure timely deliveries.
- Continuous Improvement and Process Optimization: Regularly reviewing and optimizing inventory management processes can contribute to cost reduction.
Labor and Overtime Expenses
Labor costs, including overtime expenses, have a notable impact on delivery operations. To effectively manage and reduce these costs, companies can consider the following approaches:
- Efficient Workforce Scheduling: Analyzing delivery demand patterns and aligning workforce schedules accordingly can optimize labor utilization.
- Cross-Training and Skill Development: Cross-training employees in multiple roles and providing skill development opportunities can enhance workforce flexibility and reduce reliance on overtime.
- Performance Incentives and Motivation: Implementing performance-based incentives and recognition programs can help motivate employees to work smarter and more effectively.
- Process Automation and Technology Adoption: Leveraging technology and process automation can streamline delivery operations and reduce needed manpower. Companies can invest in delivery management software, route optimization tools, and automated order tracking systems to improve efficiency and minimize labor-intensive tasks.
- Continuous Improvement and Workforce Feedback: Encouraging employee feedback and actively seeking suggestions for process improvement can help identify inefficiencies and opportunities for labor cost reduction.
In addition to these strategies, companies can embrace lean principles and waste reduction methodologies to further minimize delivery costs. By identifying and eliminating non-value-added activities, streamlining processes, and optimizing resource utilization, businesses can improve operational efficiency and lower expenses.
It is important for companies to continuously monitor and evaluate the effectiveness of their cost reduction strategies. By regularly reviewing key performance indicators and conducting cost-benefit analyses, businesses can identify areas for improvement and make informed decisions.
Integrating Capacity Planning With Demand Fluctuations
To effectively manage their operations, delivery companies must integrate capacity planning with demand fluctuations. By analyzing historical data and market trends, businesses can gain valuable insights into peak demand periods and seasonal variations. This information allows them to adjust their capacity and allocate resources accordingly, ensuring they can meet the changing needs of their customers.
Agile capacity planning is essential in today’s dynamic business environment. It enables companies to respond swiftly and adapt their operations to unexpected changes in demand. By maintaining flexibility and taking proactive measures, businesses can ensure a seamless delivery experience for customers, regardless of whether it’s during regular periods or high-demand seasons.
During peak demand periods, such as holidays or promotional events, delivery companies need to scale up their capacity to meet increased customer expectations. This involves planning ahead and allocating additional resources, such as manpower, vehicles, and warehouse space, to handle the surge in orders. By incorporating historical data and market insights into the capacity planning process, businesses can accurately forecast the expected demand and make informed decisions on resource allocation.
In contrast, during low-demand periods, companies should optimize their capacity to avoid unnecessary costs and underutilization of resources. This may involve adjusting staffing levels, consolidating deliveries, and implementing cost-saving measures. By efficiently managing capacity in both high-demand and low-demand periods, businesses can ensure operational efficiency, reduce costs, and improve customer satisfaction.
Agile capacity planning also enables businesses to respond to unforeseen changes in demand. External factors, such as natural disasters, market disruptions, or unexpected events, can significantly impact customer demand patterns. By having a flexible capacity planning framework in place, companies can quickly adjust their operations, reallocate resources, and ensure uninterrupted delivery services. This agility allows them to meet client expectations and maintain a competitive edge in the market.
Dive deeper into the world of last-mile logistics by downloading our latest white papers for free!
Delivery Profitability in Unpredictable Times
Discover strategies to navigate new trade policies and enhance your logistics operations in an unpredictable environment.
Key Benefits of a Last-Mile Routing and Dispatch Software
Enhance your delivery ROI with Routing and Dispatch Software. Learn how to make your deliveries quick, accurate, and cost-effective.
Conclusion
Capacity planning plays a critical role in the delivery industry, enabling businesses to optimize their resources, minimize costs, and deliver exceptional service. By accurately forecasting demand, analyzing resource allocation, and implementing cost reduction strategies, delivery and warehouse managers can enhance operational efficiency and provide a seamless customer experience.
To further optimize your delivery processes, consider partnering with Elite EXTRA. Their expertise and innovative tools can help streamline your operations, maximize resource utilization, and ensure successful deliveries from start to finish.
Sources
https://www.linkedin.com/advice/0/what-main-challenges-risks-overcapacity-undercapacity-1e
https://www.linkedin.com/advice/0/how-do-you-choose-best-historical-data-sources
https://www.linkedin.com/advice/0/what-main-challenges-risks-overcapacity-undercapacity-1e
https://www.investopedia.com/terms/c/cost-cutting.asp