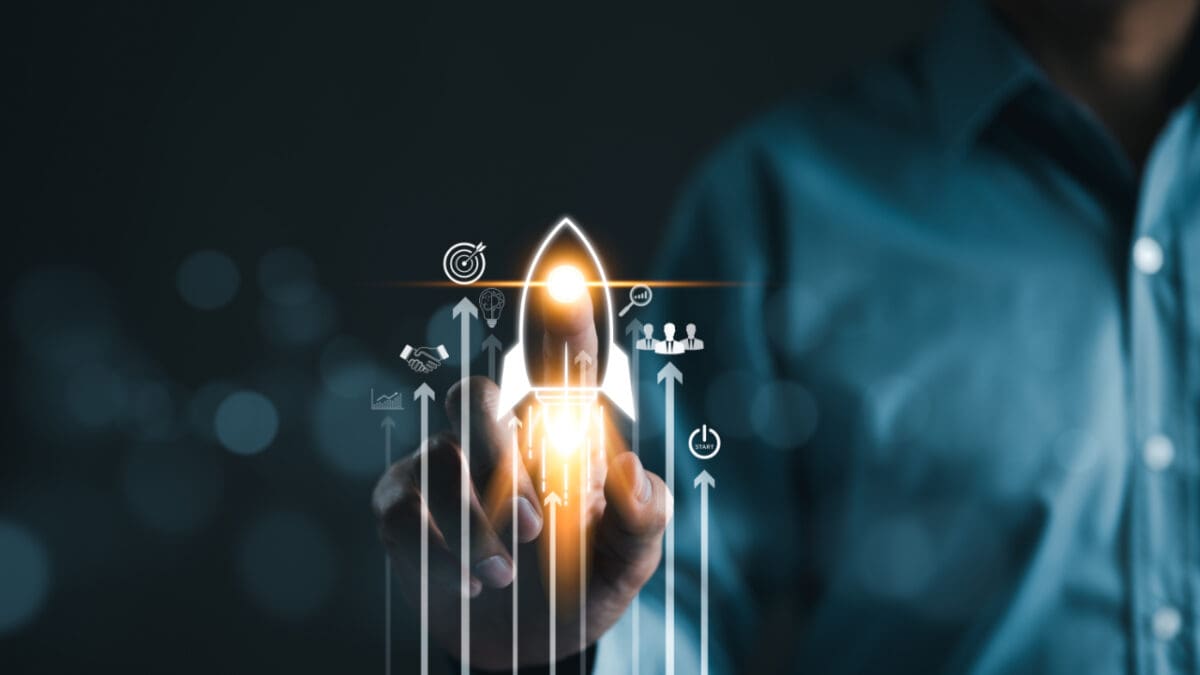
In today’s fast-paced and highly connected world, businesses of all sizes rely on efficient logistics management to ensure that goods are delivered on time, supply chains run smoothly, and customer demands are met. But what exactly is logistics management, and why is it so important for organizations to master it? At its core, logistics management involves the coordination and movement of resources—such as products, equipment, and information—from one point to another, ensuring they arrive at the right place, at the right time, and in optimal condition. Whether you’re running a small business or overseeing a large-scale operation, understanding the ins and outs of logistics management can help you improve efficiency, reduce costs, and boost customer satisfaction.
Understanding Logistics Management
To fully address the question, “What is logistics management?” it’s important to break down the process into its core components. Logistics management consists of three key elements, each of which must be carefully planned and efficiently executed to ensure the process delivers maximum benefits. These three essential components are:
1. Planning
The demand side of the supply and demand equation can often feel unpredictable, like flipping a coin to see which team gets the ball first. This unpredictability makes planning a critical component of your logistics management strategy. In stable market conditions, it’s relatively easy to maintain a consistent flow of goods and meet consumer demand. However, when demand fluctuates—either dropping or spiking unexpectedly—having a well-thought-out plan is essential.
During periods of low demand, your plan should account for efficient storage of goods until the market picks back up. On the other hand, when demand surges, you need the flexibility to ramp up production and fulfill orders promptly. Your planning process should account for these variations, ensuring your supply chain can adapt smoothly to changing conditions.
2. Implementation
Once your plan is established, the next step is execution. Implementation involves a range of actions, starting with the allocation of resources such as finances, personnel, and technology. This may require hiring specialized staff or securing partnerships with suppliers or third-party logistics providers to support your logistics operations.
Incorporating new technology can be a game-changer for logistics management. Automation of routine tasks can boost efficiency, particularly during peak demand periods. Additionally, using software that offers predictive analytics and real-time tracking can enhance your ability to respond to market demands, streamline operations, and ultimately increase revenue.
3. Control of Logistics Operations
Gaining control over your logistics operations enables your company to navigate the supply chain more effectively, minimizing disruptions and avoiding periods of unmet demand. A strong execution strategy ensures that resources are allocated properly, with clear responsibilities and timelines to guide operations. Continuous monitoring of your strategy allows for quick adjustments in response to changing market conditions.
Contingency planning plays a crucial role in risk management, helping to reduce the likelihood of supply chain failures. By developing strategies that anticipate potential disruptions, your company will be better equipped to handle unforeseen challenges. Additionally, evaluating Key Performance Indicators (KPIs) will provide valuable insights, allowing you to fine-tune operations and measure success based on the metrics most important to your business.
Different Types of Logistics
Depending on the type of business you’re in, you might find that you need to deal with different types of logistics. Most businesses have to move products and services through various types of logistics to get them from the warehouse to their customers. Here’s a closer look at the varying types of logistics:
Inbound
Inbound logistics refers to the process of managing the transportation, storage, and delivery of raw materials, components, or finished goods from suppliers to a company’s production or storage facilities, ensuring a smooth flow of resources into the business.
In 2023, the inbound logistics market size was 1.68 trillion USD. If your business produces or processes their own products, you need inbound logistics management. It determines when and how you get the goods and materials your company needs to make its product.
Inbound logistics include managing inventory levels, transportation of goods and materials, and relationships with suppliers. If you have an effective strategy in place, your company can benefit by increasing the efficiency of your production and by satisfying your customers when you meet the demand and provide a high-quality product.
Outbound
Outbound logistics focuses on efficiently delivering finished products from a business’s warehouse to customers, with an emphasis on timely and accurate fulfillment. The process begins with carefully picking and consolidating orders, ensuring large shipments are combined where possible to streamline dispatch. Once orders are picked and packed, the next steps involve shipping them to the customer and ensuring successful delivery.
A strong outbound logistics strategy enhances customer satisfaction by ensuring prompt, reliable service. By optimizing packaging, reducing shipping costs, and maintaining adequate inventory levels, businesses can not only improve customer service but also achieve cost savings. Proper labeling, tracking, and documentation are critical components of a well-executed outbound logistics operation.
Reverse Logistics
Reverse logistics is an important part of the supply chain, but often gets overlooked when it comes to ehnancement and efficiency. It is the opposite of outbound logistics; reverse logistics is the process of moving the product from the customer back to the seller or the manufacturer. These shipments can be returns or items that need to be refurbished or remanufactured. If your customer is a reseller, the reserve logistics can include products that didn’t sell or reached the end of their lifecycle.
When you develop an effective reverse logistics plan, you can minimize waste, improve supply chain efficiency, and recoup the value of returned items. You’ll find that this can also boost your customer service, especially if returns and refunds are processed smoothly.
Third-Party Logistics
Third-party logistics is exactly what it sounds like– it is when a business partners with one or many companies that provide logistics services for them. For example, companies such as FedEX, UPSP, or even Uber are third-party logistics providers.
According to IBIS World, there are over 21,000 companies in the United States offering third-party logistics (3PL) services. These providers partner with businesses to handle essential logistics tasks like shipping, warehousing, and order fulfillment. Companies such as FedEx and the United States Postal Service (USPS) play a critical role in 3PL by ensuring that products are efficiently transported and delivered to customers.
Companies like Elite EXTRA have created platforms such as Delivery Network to bring third-party providers together into one space, making them easily accessible for businesses needing quick deliveries.
In addition to shipping, 3PL providers can also offer warehousing services, storing your products until they’re ready to be shipped. These partners can also manage order fulfillment, picking, packing, and dispatching goods on your behalf. By outsourcing these logistics operations, businesses can streamline processes, reduce costs, and focus on their core activities.
Last-Mile
Last-mile delivery refers to the final stage of the shipping process, where goods are transported from the local warehouse to the customer. This critical step offers your company the chance to build strong customer relationships by ensuring timely and efficient deliveries. Although last-mile delivery is often the most expensive part of the logistics process, there are ways to optimize costs while still meeting delivery deadlines. Leveraging technology—such as route optimization and real-time tracking—can help strike the right balance between cost-effectiveness and fast delivery, keeping both your customers satisfied and your budget in check.
Responsibilities for Logistics Management
Logistics management is a complex process that involves a wide range of responsibilities, often too extensive for one person or even a single company to handle alone. Delegating these tasks effectively is essential to maintaining smooth operations. Before determining who should manage each aspect of logistics, it’s crucial to understand the key responsibilities involved. These responsibilities include:
Planning and Strategy
Planning and strategy are the cornerstones of successful logistics management; they can make or break your operations. Equally important is having a skilled and reliable team to execute and oversee these strategies. Since no two logistics processes are alike, your team must constantly assess current needs, analyze data and trends, and pinpoint areas for improvement.
If this sounds overwhelming, that’s because logistics management is a complex undertaking. This is why many companies turn to technology for assistance. By leveraging advanced tools, businesses gain deeper insights into their operations, streamline processes, and manage logistics more efficiently and effectively.
Inventory Management
Inventory management involves much more than simply ensuring that products are available on the shelves for customer shipments. This critical responsibility includes determining the optimal inventory levels based on current market trends and historical sales data.
For manufacturers, effective inventory management extends to the processes of ordering, receiving, and stocking the necessary supplies and materials. The inventory manager must conduct regular physical counts to verify that the actual stock aligns with the quantities recorded in the inventory management software. Additionally, those responsible for inventory management continuously seek to adapt and implement new policies and practices that enhance efficiency, ensuring that the inventory process remains agile and responsive to changing demands.
Transportation Management
For most companies, the person responsible for transportation management will locate and hire the shipping companies that offer the best deals and choose a warehouse to store inventory until the customer buys it. This is an ongoing responsibility as issues with timely and accurate deliveries facing challenges and rising prices may occur.
The employees responsible for transportation management will need to consistently check invoices and compare fee schedules with shipping and trucking companies. With the customer in mind, transportation management will need to closely watch delivery timelines. Customers want their products yesterday.
Order Fulfillment
Order fulfillment responsibilities cover the entire lifecycle of a product journey. From placing the order to delivery, the staff responsible for order fulfillment plays a role or needs to be aware of it. In this role, the staff member checks inventory levels and monitors delivery times for shipped orders. This job spends significant time ensuring the orders are pulled accurately, packed smartly, and shipped correctly.
While not specifically a customer service responsibility, this job, when done correctly, contributes to customer satisfaction. An accurate order that arrives in a few days generates customer satisfaction and can drive future orders.
Customer Service
Without customers, there are no orders, and a business cannot thrive. While it may not be apparent, everyone in your organization plays a role in customer service. In the context of logistics management, customer service responsibilities specifically encompass order taking, accurate order picking, and ensuring quick turnaround times for shipping and delivery.
This aspect of logistics management is primarily focused on direct customer interaction. The team members responsible for customer service strive to meet each client’s demands and expectations by ensuring products are readily available, accurately pulling orders, and selecting transportation methods that optimize both cost and shipping speed. They also manage customer expectations and relay any concerns back to management, facilitating effective communication and responsiveness.
Data Analysis and Reporting
Are you overspending on warehousing? Are your packages taking too long to reach customers? The answers to these critical questions lie in data analysis and reporting. This responsibility provides insights into the overall health of your logistics management strategy, enabling you to make informed adjustments when your current plan is underperforming.
Through data analysis and reporting, you can gain a comprehensive understanding of your logistics program. This process helps identify inefficiencies and uncover opportunities for cost savings and time reductions, ensuring that your operations remain competitive and efficient.
Importance of Effective Logistics Management
Effective logistics management delivers numerous benefits to your organization. With a well-defined logistics strategy, your business can experience:
- Improved demand forecasting and future demand planning
- Enhanced visibility throughout the supply chain
- More effective cost control measures
- Reduced inefficiencies within the supply chain
- Lower overhead costs
- Streamlined inventory levels
- Increased frequency of physical inventory checks to ensure accurate stock levels
- Reduced shipping costs
- Fewer picking and packing errors
- A competitive advantage in the marketplace
- Improved customer experiences and stronger relationships
To drive growth and increase revenue, your company needs an effective logistics management strategy. Logistics management is an ongoing process that requires regular review and adjustment to remain successful and responsive to market changes. By prioritizing logistics management, you set the foundation for sustainable success and customer satisfaction.
Want more industry insights?
Subscribe to our newsletter to receive weekly last mile logistics insights directly to your email inbox each week!
Choose Elite EXTRA as Your Partner for Logistics Management
Need help navigating logistics management? Look no further than Elite EXTRA! As your partner for logistics management, we’ll equip your business with the tools and expertise needed to streamline operations, reduce costs, and enhance customer satisfaction. Our advanced solutions provide real-time visibility into your supply chain, enabling you to make informed decisions that drive efficiency and responsiveness. With a focus on continuous improvement and innovative technology, Elite EXTRA empowers you to adapt to changing market demands and stay ahead of the competition. Partner with us to elevate your logistics management and achieve sustainable growth in today’s dynamic business environment.
Sources
https://www.statista.com/topics/7150/global-supply-chain-management/
https://www.ibisworld.com/industry-statistics/number-of-businesses/third-party-logistics-united-states
https://www.grandviewresearch.com/ industry-analysis/last-mile-delivery-market-report
https://www.mtu.edu/ globalcampus/degrees/graduate/applied-statistics/articles/disciplines
https://www.gminsights.com/industry-analysis/inbound-logistics-market