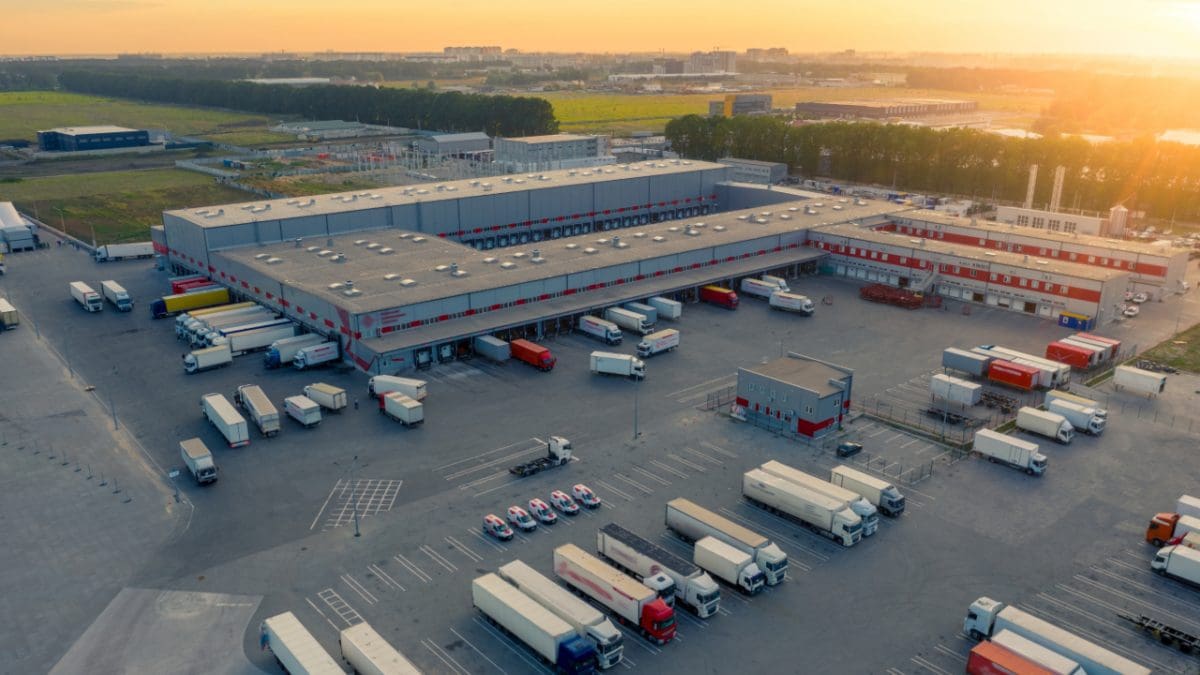
It’s easy to forget about an online package’s journey before it arrives at a customer’s doorstep. In any case, most of your online orders are home in two days or less. But have you ever wondered what happens behind the scenes? One of the most vital parts of this journey is the carrier facility.
Think of carrier facilities as the bustling nerve centers of the last-mile delivery ecosystem. These facilities process, sort, and prepare packages for their journey to the customers’ eagerly awaiting hands.
Inside these buzzing facilities, a symphony of activity unfolds. Packages zip along conveyor belts, undergo careful inspections, and are expertly sorted based on destination. It’s a whirlwind of efficiency and organization as each item finds its rightful place, ready to embark on the next leg of its journey.
Today’s guide uncovers the inner workings of carrier facilities, explores their role in the delivery ecosystem, and answers some burning questions you might have.
What is a Carrier Facility?
A carrier facility is a large warehouse or hub where packages are sorted, processed, and prepared for dispatch to a particular region. These facilities are the last stop before the package is dispatched to the customer’s doorstep.
However, some products may stop at multiple facilities if they travel long distances.
These facilities can be extensive, serving multiple geographical regions. They can also be more targeted and serve smaller areas. But the role remains the same— they help delivery companies get packages closer to the customer’s location.
Note that a delivery company, such as USPS manages a carrier facility.
What Happens in a Carrier Facility?
Carrier facilities are often 24/7 hubs. In these facilities, you will find both inbound and outbound trucks dropping off or taking customer packages to the final stretch of the delivery process.
Let’s peek behind the curtain and learn the inner workings of one of these facilities.
- Inbound trucks drop off packages meant to be delivered within the facility’s region.
- Packages are sorted, scanned, and assigned a unique tracking number.
- Designated machinery and employees then inspect the packages. They check for damages and discrepancies and verify content.
- Next, the packages are stored accordingly. For instance, some packages may require storage in darkrooms, refrigerators, or freezers. Other packages might be loaded immediately into outbound trucks for delivery.
- Once packages are ready for delivery, carrier facilities use sophisticated algorithms to determine the most optimal shipment routes.
- Outbound trucks transport the packages to their respective destinations. The destination could be the customer’s address or one more stop at another facility. Packages bound for the same location will be consolidated when possible.
- Throughout the entire process, carrier facilities track and document the movement of each package. This includes scanning barcodes, updating tracking information, and generating documentation such as shipping labels and invoices. These records enable real-time tracking for customers and help address problems that may arise.
Examples of Carrier Facilities in the US
For this section, we’ll use examples of three delivery companies in the US.
1. USPS Carrier Facility
The United States Postal Service (USPS) operates a network of processing and sorting centers nationwide. These facilities are vital in handling and sorting mail and packages across different regions.
Packages can stay for up to 2 days at USPS regional carrier facilities before dispatch to the next location.
2. UPS Carrier Facility
Like other delivery companies, UPS has several carrier facilities serving specific regions. The UPS regional facility is often the last stop before customers receive their packages. But, the package might go through multiple UPS-operated facilities before arriving at the customer’s location.
3. FedEx Ground Distribution Centers
FedEx Ground operates numerous carrier facilities across the United States. These facilities serve as regional hubs for package sorting and distribution. Packages are received from various origins, sorted based on their destinations, and dispatched to local delivery depots for final-mile delivery.
These are just a few examples. Different carriers and logistics providers may have their own unique facilities and operations based on their scale of operations and geographic reach.
Carrier Facility Notifications
Carrier facility notifications are alerts or updates these facilities provide to customers or business owners, informing them about the status or location of their packages within the hub.
Like most last-mile delivery notifications, the goal is to provide more visibility into the delivery process. Specifically, these notifications enhance the customer experience and reduce delivery anxiety.
Below are four examples of notifications you can receive from a carrier facility.
1. The Package Has Arrived at the Carrier Facility
Customers may receive a notification when their package arrives at a carrier facility. This alert indicates a package has reached a specific hub or sorting center. Often, the package will stay at the sorting center for a few hours or two days at most before moving to the next destination.
2. Package Transferred to Another Carrier Facility
Customers receive this alert when the package leaves the carrier facility for final-mile delivery. The customer will be informed that the order has been transferred to another facility or their address. If the latter, the notification will read as “out for delivery” and include the earliest arrival time (EAT) details.
3. Delay in Order Processing
These alerts are rare and most common when there’s an unavoidable delay in sorting and processing at carrier facilities.
4. Parcel is Being Processed at Carrier Facility
This notification simply informs the customer that the package is at a certain carrier facility and is undergoing processing, such as barcode scanning or sorting.
The Role of Carrier Facilities in Last-Mile Delivery
Carrier facilities are vital linchpins in last-mile delivery. How so? These facilities ensure customer packages reach their doorstep in prime conditions and on time. They also act as strategic nerve centers where packages are sorted, organized, and dispatched to local delivery locations.
But the facilities are more than just sorting hubs. They are the connective tissue that binds the entire delivery ecosystem together. They act as essential intermediaries, coordinating between online retailers, shipping companies, and local carriers to ensure packages travel smoothly.
Before we dive into the specifics, let’s find out the main users of these facilities.
Who Uses Carrier Facilities?
These facilities are used by various entities involved in transporting and delivering goods and services.
1. Postal Services
National postal services like USPS use these facilities as key processing and distribution centers. Postal services count on carrier facilities to sort, route, and dispatch mail and packages within their respective countries or regions.
2. eCommerce Retailers
Online retailers, such as Amazon, Walmart, and eBay, use these facilities extensively. These retailers leverage them to manage their inventory, consolidate shipments, and coordinate the last-mile delivery of products customers order.
3. Shipping and Logistics Companies
Major shipping and logistics companies like FedEx, UPS, DHL, and USPS rely on carrier facilities. They use them as central hubs for sorting, processing, and dispatching packages. For these companies, the facilities are a way to streamline operations and ensure the efficient movement of shipments within their networks.
4. Third-Party Logistics Providers
3PLs use carrier facilities to handle the transportation and distribution of goods on behalf of their clients. They leverage them to consolidate shipments, optimize routes, and ensure efficient delivery operations.
5. Freight Forwarders
Freight forwarders depend on these facilities for consolidating and distributing shipments. They leverage these facilities to facilitate freight movement.
6. Local and Regional Carriers
Local and regional carriers— often contracted by eCommerce retailers— use carrier facilities as shipment pickup points. These carriers depend on them to access packages, load them onto their vehicles, and deliver them to customers’ doorsteps within specific regions or neighborhoods.
How Carrier Facilities Support Last-Mile Delivery
Carrier facilities are key contributors to the success of last-mile deliveries. Here’s why:
Sorting and Consolidation in Carrier Facilities Reduces Costs
Carrier facilities are the central hubs where packages from various sources are received and sorted based on their final delivery destinations. This efficient organization and preparation guarantees that customers will receive the correct order without the risk of damage. Conversely, consolidation enables products to reach customers faster while reducing the costs associated with final-mile shipping.
Routing and Optimization Speeds up Delivery
These facilities do more than just sort and prepare packages for shipping. These facilities also work with advanced algorithms to determine the best optimal routes. The route optimization technology considers weather, traffic conditions, delivery schedule, and customer proximity. In turn, customers receive goods faster, and last-mile delivery stakeholders save costs.
Local Carrier Coordination Enhances Package Distribution and Delivery
Carrier facilities often collaborate with local delivery partners or independent contractors responsible for the actual doorstep deliveries. These collaborations allow seamless handoffs and efficient distribution of packages.
Tracking and Updates Keeps Customers in the Loop
Carrier facilities also help keep customers updated about their package’s status. For example, when a package arrives at the facility, the customer receives a notification. Customers also get updates when the package leaves or when delays happen.
Generally, carrier facilities are pivotal hubs that optimize and streamline the last-mile delivery process.
They ensure efficient sorting, routing, and coordination, leading to faster, more reliable deliveries. And as you know, faster deliveries help build a more favorable customer experience. In fact, a 2019 study found that 62% of customers define faster shipping times as the epitome of a great shopping experience.
What to Expect From Carrier Facilities in the Future
Like other aspects of the delivery ecosystem, we expect to see carrier facilities undergo a major transformation. Let’s touch on this briefly.
- Increased Adoption of Automation and Robotics: These facilities will increasingly adopt automation and robotics technologies to streamline operations and improve efficiency. Some expected technologies include robotic arms for package handling, automated sorting systems, and autonomous vehicles for intra-facility transportation. Companies like FedEx have already introduced intelligent sorting robots in Singapore and South China. These automations will reduce manual labor, improve speed, and minimize errors.
- Data analytics and artificial intelligence (AI): As AI brings disruptive transformation in other sectors, carrier facilities will not be left behind. Many facilities will leverage AI superpowers to enhance the overall last-mile delivery experience. Specifically, AI will help these facilities manage package processing and improve route planning.
- Sustainable Practices: As sustainability grows in popularity, these facilities will implement eco-friendly measures. We expect to see them adopting electric vehicles for transportation, relying on renewable energy sources, and implementing waste reduction and recycling initiatives.
Frequently Asked Questions
1. How Do Carrier Facilities Facilitate Faster Last-Mile Deliveries?
Carrier facilities centralize the package sorting process based on the designated location of packages. This reduces travel distances and ensures faster delivery times. Also, these facilities have established partnerships with local carriers. In turn, this allows for quick handoffs and streamlined last-mile operations.
2. What Security Measures are Implemented in Carrier Facilities to Protect Packages?
These facilities enforce vital measures such as comprehensive surveillance systems, access control systems, and package tracking technologies.
3. How Do Carrier Facilities Handle Returns and Exchanges?
When a package is returned, it is inspected to ensure its condition aligns with the return policy. The carrier facility then processes the return label and coordinates with the shipping company for reverse logistics. It also initiates timely refunds or exchanges.
4. What is the Difference Between Carrier Facility vs. Distribution Center Vs. Warehouse?
A carrier facility is often the final stretch before customers receive their goods. The facility sorts, processes, and prepares packages for dispatch to the customer’s address.
Contrarily, a distribution center is a facility that stores inventory briefly until the orders are fulfilled. On the other hand, warehouses work like distribution facilities, but they keep inventory longer.
5. Can Customers Collect Packages from a Carrier Facility?
No. Customers can not collect their packages from these facilities since they are not designed to be customer-facing.
Final Remarks
As a customer or business owner, you won’t have much control over what happens at a carrier facility because they are managed by delivery companies. However, businesses working closely with these facilities can still ensure customers get the best shipping experience by working with a reliable delivery and logistics partner.
In addition, delivery and logistics companies can proactively prioritize their customer experience by investing in automation, routing, and dispatch technology to run their carrier operations.
For overall more efficient deliveries, reach out to Elite EXTRA today.
Sources
https://www.insiderintelligence.com/