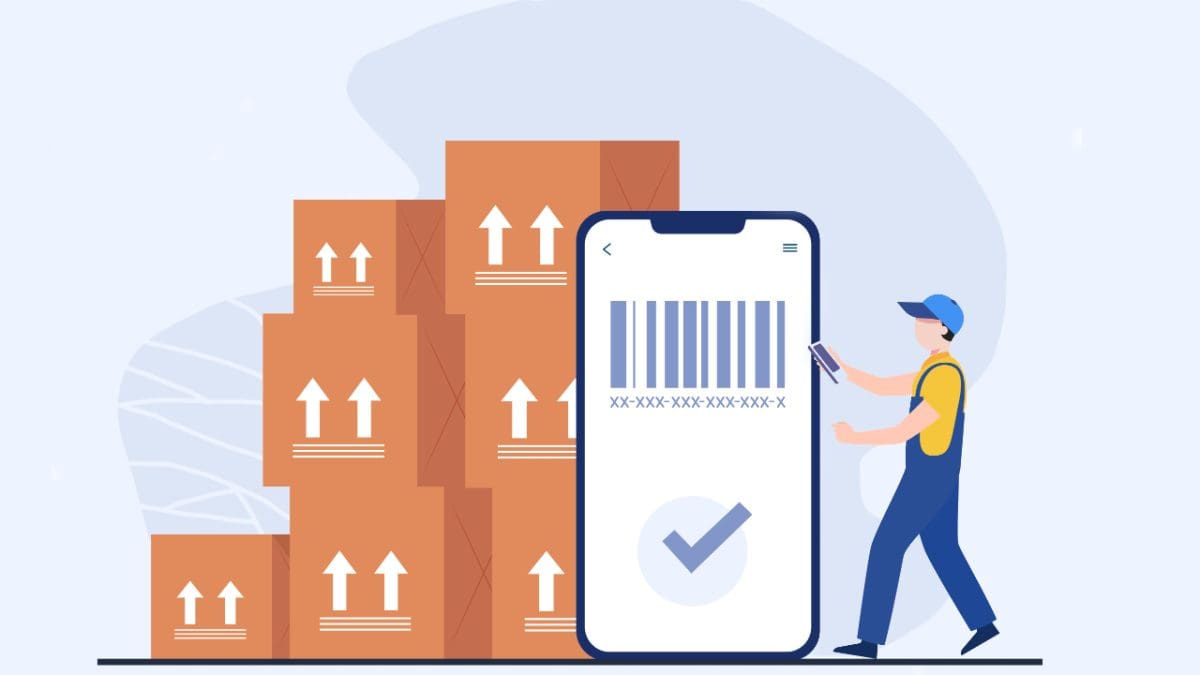
When it comes to logistics and delivery, efficiency and accuracy are key. That’s where barcode tracking comes into play. As a technology that’s revolutionized the way we manage and monitor goods, barcode tracking is an important tool in the modern supply chain.
Barcode tracking isn’t just about scanning a series of lines and numbers. It’s a sophisticated method of capturing data and transforming it into actionable insights. By utilizing barcode tracking, companies can have real-time access to information about their products, from the moment they leave the warehouse to the instant they reach the customer’s doorstep. The technology provides transparency, enabling businesses to optimize routes, reduce errors, and enhance customer satisfaction. It’s made last-mile delivery more agile and adaptable, meeting the ever-increasing demands of the contemporary consumer.
Today we’re taking a closer look at barcode tracking. We’ll explore its functionalities, benefits, and challenges, and how it can be integrated into various business models. Whether you’re a logistics manager or a decision-maker in the industry, understanding barcode tracking is the key to unearthing new potentials in your operations.
Understanding Barcode Tracking
The logistics and supply chain landscape is rapidly evolving, and at the heart of this transformation lies barcode tracking. Let’s examine barcodes, how they work, the types used in logistics, and the benefits that make them indispensable.
What Are Barcodes & How Do They Work?
Barcodes are visual, machine-readable representations of information. Imagine them as a unique fingerprint for products and packages, made up of lines and spaces of varying widths.
Here’s how it works:
- Encoding: Information is translated into a pattern of bars and spaces.
- Printing: This pattern is printed onto labels or directly onto items.
- Scanning: Using optical scanners, the pattern is read, and the information is retrieved.
Types of Barcodes Used in Logistics
Different logistics operations require specific types of barcodes. Let’s explore some commonly used ones:
- 1D (One-Dimensional) Barcodes: These are the traditional barcodes you likely see on most products. Example: UPC (Universal Product Code).
- 2D (Two-Dimensional) Barcodes: These contain more information and can be read from different angles. Example: QR codes.
- 3D (Three-Dimensional) Barcodes: Emerging technology that adds another data layer through height and depth. Still experimental in some sectors.
- RFID (Radio-Frequency Identification) Tags: Though not a traditional barcode, RFID tags communicate data via radio waves, offering greater tracking capabilities.
Advantages of Barcode Tracking
Barcode tracking offers compelling advantages for logistics managers, presenting a set of powerful solutions for various needs. Quick scanning speeds up processing, saving valuable time, and enhancing overall efficiency. This speed, combined with the reduction of manual entry errors, ensures precise data collection and greater accuracy.
The real-time tracking capability offers complete visibility, transforming inventory control and allowing managers to have up-to-date information at their fingertips. This constant access to data is supported by the relatively inexpensive nature of printing and managing barcodes, making it a cost-effective solution for businesses.
The adaptability of barcode tracking is evident in its scalability. Whether it’s a small business or a large enterprise, barcode systems can be tailored to fit various needs and sizes, providing a versatile tool that grows and evolves with the business. Overall, the highlights of barcode tracking point to a technology that’s indispensable in modern logistics, offering a pathway to streamlined operations and strategic growth.
From the simplicity of 1D barcodes to the sophistication of RFID tags, these tools serve as the silent workhorses that drive accuracy, efficiency, and visibility in logistics.
Implementation
The implementation of barcode tracking is a strategic move that can streamline logistics processes. Whether you’re new to this or looking to enhance existing systems, let’s explore how you can integrate with Warehouse Management Systems (WMS), generate and label barcodes, and make use of scanning devices and technology, including Elite EXTRA’s capabilities.
Integrate With Warehouse Management Systems (WMS)
WMS (Warehouse Management System) integration is the cornerstone of successful barcode tracking, serving as the central hub that aligns inventory, picking, packing, and shipping processes.
The first step in achieving this integration begins with a thorough assessment of your warehouse’s specific needs and goals. It’s crucial to have a clear understanding of what you want to accomplish with the barcode tracking and how it will fit into your existing operations.
Next, selecting a WMS that aligns with your requirements is vital, and ensuring that it supports barcode tracking is non-negotiable. This alignment with your warehouse’s needs ensures that the system will be a fitting and productive part of your process.
Following the selection of a suitable WMS, seamless integration of your existing data with the system is essential. This data synchronization ensures that everything is aligned and ready for the tracking to begin, setting the stage for a smooth transition.
Finally, training your staff to equip them with the knowledge to utilize the integrated system effectively is very important. Investing in proper training ensures that everyone is on the same page and able to leverage the power of barcode tracking to its full potential. Together, these steps create a roadmap for implementing a successful barcode tracking system through WMS integration, paving the way for optimized logistics management.
Barcode Generation and Labeling
The core of barcode tracking lies in generating and affixing labels, a process that requires careful planning and execution.
First, you’ll need to select the appropriate type of barcode based on your specific needs. This might be a one-dimensional barcode (1D) for simpler applications or a more complex two-dimensional (2D) code, depending on the information you need to encode.
Next, utilizing specialized software, you will create the barcodes for each product. This software translates the product information into a scannable format that can be read by the corresponding hardware.
Printing the labels requires specialized printers that ensure quality and readability. The clarity of the barcode is vital, as any errors in printing can lead to scanning issues down the line.
Finally, you’ll affix the labels to the products, ensuring consistency in placement. This step may seem trivial but is essential for smooth scanning and tracking. A standard placement allows for efficient and error-free scanning.
Creating an effective barcode tracking system is a carefully sequenced process that involves selecting the right barcode, generating it using specialized software, printing it with quality, and applying it consistently. It’s a process that, when done right, can significantly streamline inventory management and tracking across various stages of the supply chain.
Scanning Devices and Technology
Scanning technology has come a long way, and its selection can be as customized as the products you handle.
- Handheld Scanners: Versatile and ideal for on-the-go scanning.
- Fixed Scanners: Positioned at strategic points for automated scanning.
- Mobile Scanning Apps: Utilize smartphones for flexible scanning options.
Elite EXTRA has added a dimension to barcode scanning by incorporating this technology into its last-mile delivery software and making it accessible for drivers through its mobile app. Why is that a game-changer for deliveries?
- The integration with existing systems throughout the supply chain is a leading benefit, as it allows barcode scanning to be seamlessly integrated into operations and enhances tracking with ease.
- Real-time tracking is another vital feature, offering immediate visibility into last-mile delivery operations. This ongoing insight helps managers make informed, timely decisions that can have a significant impact on efficiency and effectiveness.
- Enhanced customer service is also a major benefit. By improving accuracy in tracking and delivery, customer satisfaction is enhanced. Precise information and timely deliveries build trust and can lead to increased loyalty and repeat business.
Benefits of Barcode Tracking in Last-Mile Delivery
Barcode tracking is a crucial need in logistics, especially when it comes to last-mile delivery. This is the stage where the product reaches the consumer, a point where accuracy and efficiency are paramount. What tangible benefits does barcode tracking bring to this vital phase?
Enhanced Package Traceability
Barcodes enable continuous tracking of packages, providing real-time updates at each stage of delivery. It allows for a level of real-time monitoring that ensures efficiency and accountability. This ease of access allows both the delivery team and customers to effortlessly monitor package status, fostering transparency and trust in the delivery process. Barcodes uniquely identify packages, ensuring they reach the right destination without mix-ups.
Reduced Delivery Errors
Barcoding transforms the manual handling process by automating it, significantly reducing the chance of errors that can lead to delays or misplaced deliveries. Even if an error occurs, real-time tracking ensures immediate correction, minimizing any delays and maintaining the efficiency of the delivery process. This precision not only streamlines operations but also bolsters customer trust and loyalty. The combination of error elimination, quick correction, and accuracy in delivery converges to increase customer satisfaction, strengthening relationships with clients and enhancing the overall reputation of the delivery service.
Efficient Route Planning and Optimization
Barcode tracking revolutionizes the delivery process through dynamic planning, allowing for real-time adjustments to routes that avoid delays and obstacles. This adaptability not only streamlines the delivery but also contributes to fuel and time efficiency, creating a more sustainable and profitable operation. The inherent flexibility of barcode tracking means that if a change is needed mid-route, quick rerouting is possible, maintaining the overall efficiency of the delivery process.
Data Analytics
Barcode tracking serves as a robust tool for generating insightful reports filled with data that paints a detailed picture of delivery performance, trends, and areas for growth. This wealth of information paves the way for informed, data-driven decision-making within the business, pinpointing both successes and challenges. The result is a uniquely tailored customer experience, where services are customized to meet individual preferences and expectations. By harnessing the power of data analysis, businesses not only enhance efficiency but also create a more resonant and satisfying connection with their customers, strengthening loyalty and trust.
The benefits of barcode tracking in last-mile delivery aren’t just a matter of convenience; they shape the entire customer experience. From the traceability of a package to reduced errors, optimized routing, and insightful analytics, barcode tracking translates into efficiency, reliability, and a competitive edge in the market.
Challenges of Implementing Barcode Tracking
The integration of barcode tracking in last-mile delivery is a promising development in the logistics industry. But, implementing this technology comes with its own challenges. By understanding these hurdles ahead of time, organizations can develop strategies to overcome them, making the adoption of barcode tracking smoother and more effective.
Barcode Legibility
Barcodes are integral to modern logistics, but challenges like physical damage, printing issues, and environmental factors can cause problems. Barcodes that become smudged, torn, or worn out, poorly printed ones with faded ink or low contrast, and those affected by extreme weather conditions like heat or humidity can lead to delays and inefficiencies.
But, these hurdles aren’t insurmountable. By investing in high-quality printing materials, ensuring proper placement of barcodes, and taking protective measures against environmental factors, these issues can be substantially mitigated. The proper handling of barcodes fosters a more efficient and responsive delivery process, translating into higher customer satisfaction.
Training and Adoption by Delivery Personnel
Implementing barcode tracking can face resistance, especially from staff accustomed to older methods. Plus, the proper use of barcode scanning devices necessitates dedicated training. A lack of such training could result in mistakes and inefficiencies. Organizing effective training sessions also requires time and investment, which can slow down the process. But, these challenges can be addressed by gradually introducing the technology, providing hands-on training, and communicating clearly about the benefits. Such an approach fosters a smoother transition, capitalizing on the robust advantages of barcode tracking to optimize efficiency and accuracy in logistics.
Bridging the Gap: Strategies for Success
- Select Quality Materials: Investing in quality barcode labels and printing technology minimizes legibility issues.
- Implement Thorough Training: Develop comprehensive training programs tailored to your team’s needs. Support them throughout the transition and provide ongoing training as needed.
- Engage and Communicate: Explain the benefits and the rationale behind the change. Involving staff in the process and addressing their concerns builds trust and acceptance.
- Invest in User-Friendly Technology: Choosing devices and software that are user-friendly can reduce the learning curve.
Challenges in barcode legibility and training are not insurmountable. With foresight, proper planning, and a genuine understanding of the concerns of the delivery personnel, these challenges can be transformed into opportunities for growth and efficiency.
Conclusion: Transforming Last-Mile Delivery with Elite EXTRA
Implementing barcode tracking in the last-mile delivery process is a strategic move that businesses can make to enhance efficiency, accuracy, and customer satisfaction. While there may be challenges such as barcode legibility and training needs, these can be effectively addressed with careful planning and the right support.
Looking to streamline your logistics with advanced barcode scanning capabilities? At Elite EXTRA, we integrate barcode scanning into our last-mile delivery solutions to provide unparalleled efficiency and accuracy. From scanning barcoded invoices to real-time tracking and warehouse picking, our system is tailored to fit your specific needs. With our customization options, including Regex codes, and seamless integration within existing workflows, we offer a solution that will elevate your operations. Whether you’re handling tasks like order verification, label creation, or signature and photo capture, our barcode scanning technology ensures precision and adaptability.
Contact us today to learn more about our barcode tracking options and discover how we can help you optimize your delivery process, reduce costs, and exceed customer expectations!
Sources
https://electronics.howstuffworks.com/
https://www.digitaljournal.com/pr/the-benefits-of-barcode-scanning-for-your-warehouse
https://www.fool.com/the-ascent/small-business/inventory-management/articles/barcode-inventory-system/
https://www.shopify.com/retail/barcode-faq