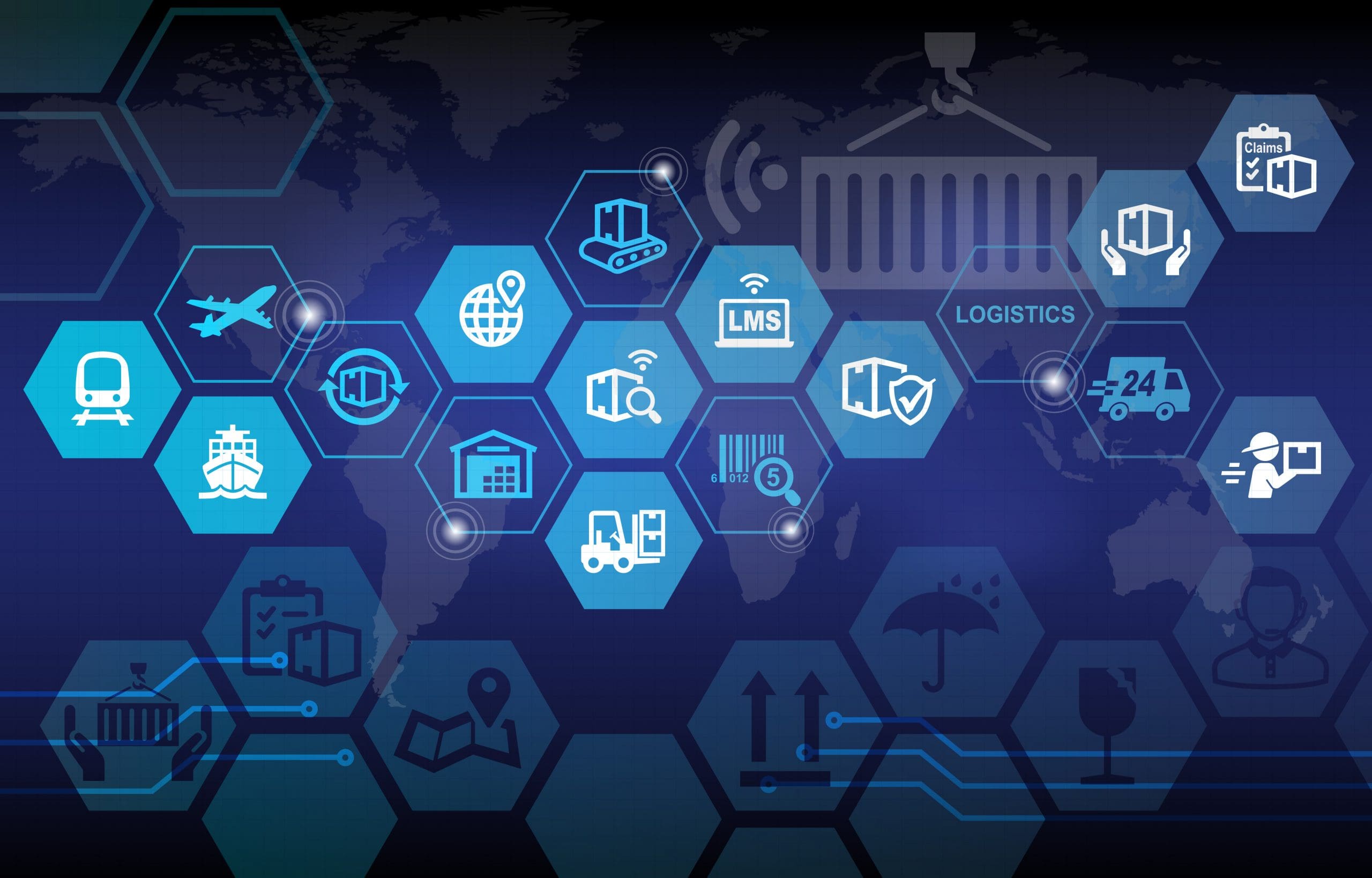
Reverse logistics is the term used to describe operations related to the return and reuse of products and materials. It is the process of moving or routing goods to be returned, recalled, damaged, or found needing repairs from their current location to a destination for the purpose of recapturing value from products, such as restocking, repackaging, salvaging parts, recycling, or proper disposal.
Reverse logistics has existed in waste and recycling industries for decades. Typically, it has focused on simply an accumulation of unsorted bulk materials for delivery to a disposal or sorting facility. Materials sorted for reprocessing are then dispatched to an appropriate location.
There are several differences in the process in the fulfillment and logistics industry. First, the items are generally intact, often in the original shipping package. The items are not mixed and can be routed individually to the appropriate destination. In addition, the customer is likely to be directly available for communication on the condition of the item and the reason for the return. These facts allow for detailed individual control in the reverse logistics process but are also more costly. In addition, reverse logistics supply chains require, on average, up to 20% more space and labor capacity when compared to forward logistics. However, compared to forward logistics, reverse logistics are generally not as time-sensitive and may not require strict, up-to-date tracking.
Deployment Channels in Reverse Logistics
There are six general channels in the reverse logistics process: Returns, recalls, repairs (refurbishment, re-use, or re-manufacturing), repackaging (for restock or resale in secondary markets), recycling, and disposal. A final option for situations where the cost of shipping is more than the item’s value is to let or convince the customer to keep the item, either by steeply discounting it, or refunding the price. Obviously, there are drawbacks to this option, but when minimizing costs, it may be the best course in some instances.
Customers return products for a number of reasons. An item may be defective, damaged, seasonal, or simply fails to meet expectations. Regardless, the key to handling returns efficiently is having streamlined, customer-friendly processes for relabeling and return shipping products. There are several strategies for this: a return label can be included in the shipment and it can be picked up by the original shipper, the customer can drop off the item at a brick and mortar outlet, or return it to a shipper or retailer with a prearranged processing agreement.
Retailers are developing relationships with existing brick and mortar retailers to receive and process returns, such as Amazon partnering with Kohl’s to accept returns. In addition, businesses are being created for the sole purpose of accepting and processing returns. These agreements can involve return authorizations, merchandise verification, and tracking processes. Vendors are finding cost savings in separating reverse logistics from forward logistics.
Experts advise, if possible, returning the item to a physical location where it can be evaluated for damage, overly hard use, functionality, and to create an opportunity to question the customer on the reason for the return. Alternatively, efforts should be made to learn the reason for the return through email or another method.
Returns
The simplest route for returning intact merchandise is direct shipping to the distribution warehouse where it can be placed back in inventory for reshipment. The key is to assure the condition is “like new” and keep repackaging to a minimum.
Recalls
Another reason products are returned is through recalls. If a product has been determined to have a systematic defect, potential hazard, subject to government regulations, liability concerns, or reporting requirements it can be recalled. This is a critical reverse logistics category since it may pose liability, compliance, or other legal consequences.
High-tech devices are typically recalled because of faulty electronics, construction issues, problems with batteries, or other potential hazards. The key is to have processes in place to locate and notify customers possessing these products and persuade and instruct them how to return the device. This reverse logistics channel must specifically direct the merchandise to an appropriate facility where it can be repaired, retooled, or disposed of so removal from use can be documented.
Repair, Refurbishment, or Re-manufacturing
Not all defective products that are returned go directly to disposal. If the faults are not too severe, manufacturers can identify failures or damage and recondition the product to like-new condition and return it to stock. These items can be resold as reconditioned or remanufactured. Conceivably, this process can reclaim significant value from the product and avoid disposal costs.
These practices are becoming more common as manufacturers recognize the value of reusing materials from returned goods and help recoup reverse logistics costs and also advance sustainability efforts. It is becoming common to see online vendors carrying merchandise labeled as “reconditioned or remanufactured.” Quite often, these items carry a new or limited warranty.
This reverse logistics channel must contain a streamlined process to identify, separate and direct items that can be efficiently reconditioned to an appropriate facility. Again, return authorizations, merchandise verification, and tracking processes are needed to monitor flow in the pipeline. Also, the repair or refurbishment procedure must focus on cost management.
Repackaging for Restock or Resale in Secondary Channels
Approximately 95% of products are returned simply because customers are dissatisfied with them and not because there’s something wrong with them. These products are typically returned to the warehouse and repackaged for return to inventory and resale. Products with minor flaws may be repaired, reconditioned and repackaged for resale in secondary markets. Typically these products end up in online sites, discount retailers, and bulk sellers. Again, this process can reclaim significant value from the product and avoid disposal costs.
Reclaiming, Recycling, and Disposal
The reverse logistics process focuses on recovering and minimizing costs from returned items. In cases where it is not possible to repair or repackage items, the last resort may be reclaiming usable materials and disposing of unusable parts. Current attitudes are emphasizing sustainable practices and recycling has become a means of recovering valuable materials and limiting costs.
In particular, high-tech products can hold valuable materials. Circuit boards contain rare earth metals such as gold, silver, titanium, palladium, or copper. Batteries can be recycled and can contain materials that if disposed of in the normal manner can possibly contaminate soil or water. Significant savings can be achieved by reclaiming these metals and other materials.
Each of these are categories of reverse logistics that introduce challenges and opportunities for your delivery business.
Learn more by downloading our complete whitepaper on this topic.